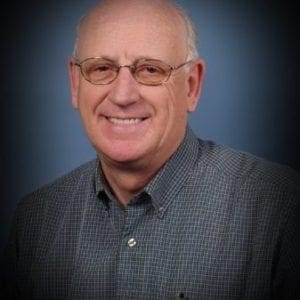
We continue to get great reader comments on A 60 year Perspective on Billboard Structure Construction.
Productivity Fabricators Jon Odom says wind load and the job site impact billboard costs
There are several factors that contribute to billboard costs, the biggest is the wind load for the location, in most areas the code wind load is 115 MPH, however, in southern FL (Miami) it is 175 MPH the same sign there will cost about twice as much as in the 115 MPH areas. Other coastal areas range around 150 MPH.
The second factor is the jobsite itself. The soil conditions can drive the foundation cost three of four times higher than a “normal” foundation would cost. A jobsite in an open area with room for equipment and space for assembly will cost much less than a tight location.
Some ways to keep the cost down are:
(1) Do not build any taller than absolutely necessary.
(2) Build straight back to back (not V ) when possible.
Kennedy Outdoor Founder Richard Kennedy says you can keep costs down by doing things in-house and owning your equipment

One thing that has helped keep our construction costs down is having our own equipment. We have a small little crane truck as well as excavators of various sizes. You can get a lot of money wrapped up in the footer if you have to have it drilled or if you have to hire someone to excavate the hole for you. In most cases, we can set the column in the ground with our small crane as well.
I realize however that some locations will only allow for a drilled style footer and our crane may be too small to set larger and longer column sections. Most of our boards are not that tall, fortunately.
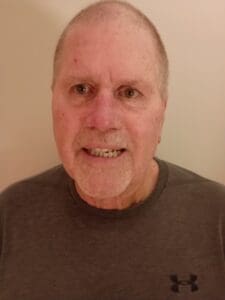
Glenn Hills at Cross Light Construction says build costs are increasing
I have built over 600 steel I- Beam 14’x48′ sign structures and over 3000 10’x36′ & 14’x48′ steel Mono-pole sign structures since 1973. Mr. Barnes you have done a great job building over 10,500 signs in your career.
In 1973 First steel I beam structure 14’x48′ back to back 60′ overall height steel and labor with our own crane & welder. 3 man crew $9,000 total cost. Cost for same job in 2025 for a 14’x48′ 60′ OAH Five I- Beam structure back to back steel faces with walkways & 3 men, crane, welder, drilled footings, concrete, permits, & surveying $87,000
First steel mono pole built in 1980 14’x48′ 55′ OAH back to back Full Flag with labor and power $23,000. In 2025 One steel mono-pole 14’x48′ center mount 55′ OAH 20’V back to back drilled footing depth 5′ wide 33′ deep with concrete. 3 men one 40 ton crane to erect sign and one 75 Ton crane to set top head Three LED light fixtures per side with conduit & wiring. $112,000 with all permits & surveying. Does not include Land Lease.
To receive a free morning newsletter with each day’s Billboard insider articles email info@billboardinsider.com with the word “Subscribe” in the title.Our newsletter is free and we don’t sell our subscriber list.
Paid Advertisement